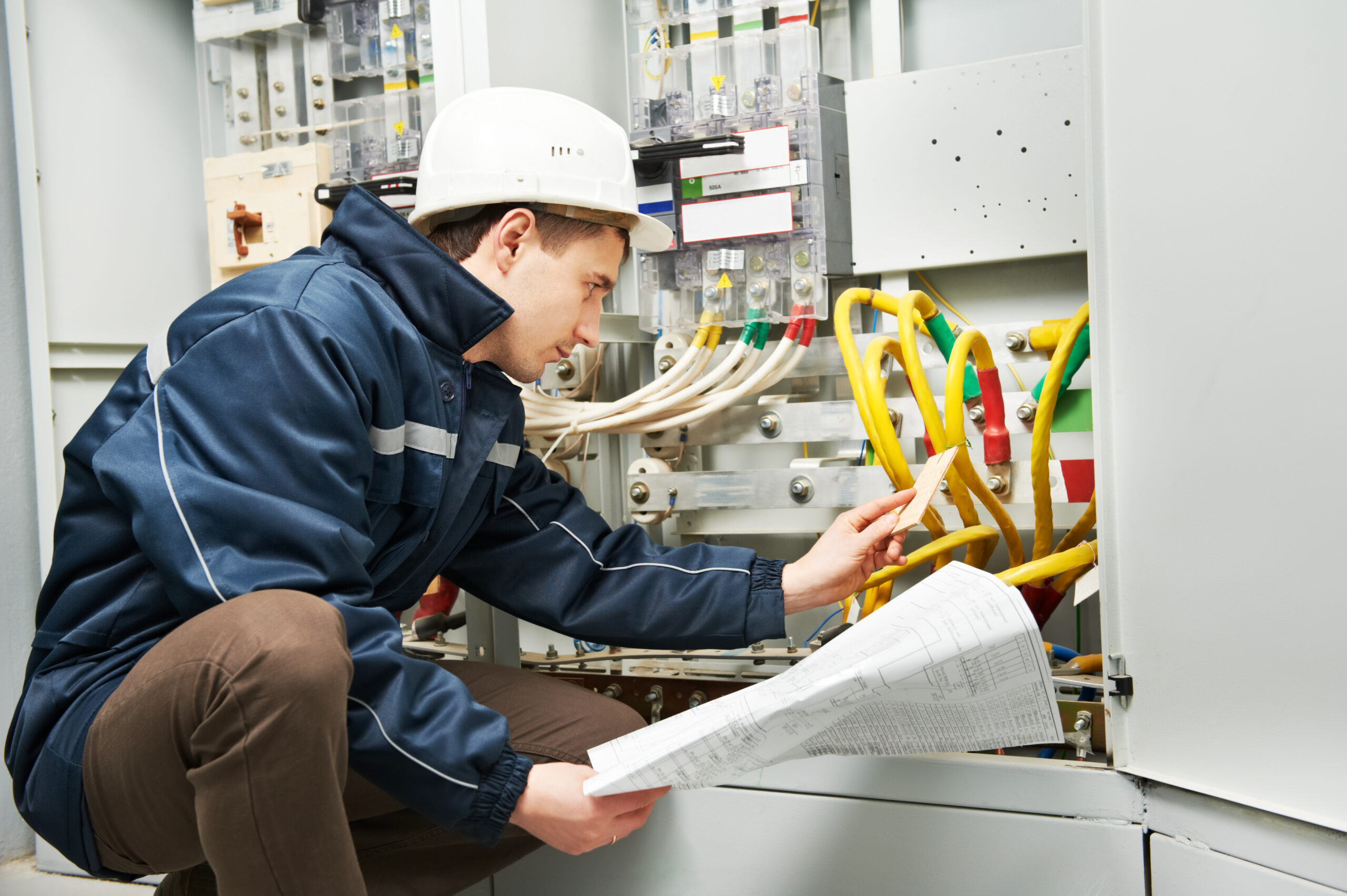
Design for Maintenance
Introduction
From 2016 to 2018, the United States experienced an increase in energy expenditures. This increase reached $1.3 trillion. From data provided by the U.S. Energy Information Administration’s (EIA) State Energy Data System (SEDS), this amount was nearly a $200 billion increase. During this time period, energy consumption and average energy prices increased faster than the United States’ population and gross domestic product. The amount of money spent on all energy used in businesses, offices, homes, industrial facilities, and vehicles, increased from $3,215 per person to $3,891 per person by 2018, a 16% increase (per state, this varies depending on the amount and availability of natural gas appliances and services).
Regardless of state, the use and cost of electricity is no small sum. It's no wonder that in architecture and engineering, energy reduction strategies and energy efficiency are among some of the most important contributors for best practice design. When designers talk about energy reduction, the conversation tends to gravitate towards a tight envelope, solar panel design, and efficient equipment. But both buildings and equipment require maintenance. Without maintenance, what was once an energy efficient design component can become a hinderance to the overall energy savings strategy.
How Equipment Maintenance Fits Into the Equation
When equipment is new and installed properly, it can operate at its performance and energy consumption benchmarks. If not properly maintained, equipment performance and energy consumption can be affected. This is especially true for rotating equipment such as fans and pumps. Over time, energy bills and equipment's runtime testify to the effectiveness of the current maintenance program.
Market Sector Applications
Commercial
In some commercial buildings heating, ventilation, and air conditioning (HVAC) equipment can account for 50% of the total energy consumption. Ironically, the same equipment may comprise 15% to 20% of total ownership cost. The energy costs may represent 70% to 80% of an HVAC system operating cost.
There are a number of studies available that discuss a quantified increase or decrease in energy use via good or poor maintenance practices. Good maintenance practices utilized on HVAC equipment can save between 10% and 30% when compared to neglecting maintenance, and repair and maintenance account for even more revenue loss.
Industrial
Within the Industrial industry, there is typically a larger amount of energy conservation at stake due to the run time requirements and the motor sizes. In a case study of a motor system, the impact of equipment maintenance was measured in a relationship of performance vs. energy savings potential. The below graphic illustrates the results.
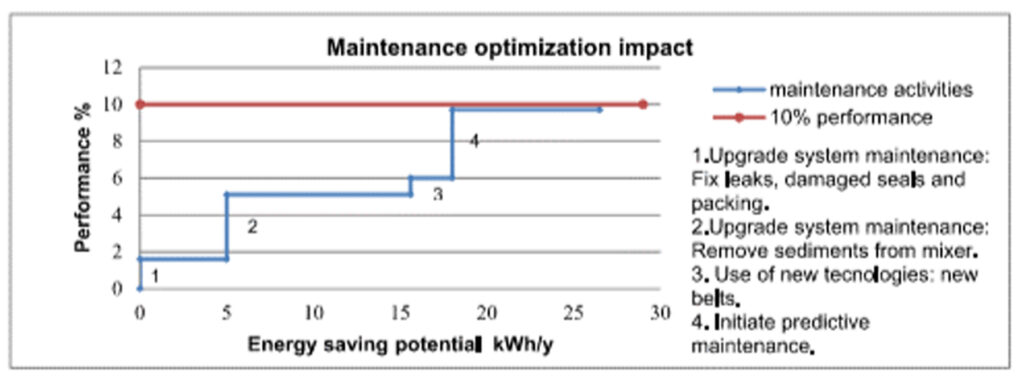
The study showed that sustained system energy performance could be achieved by standard maintenance practice. Although each piece of equipment should be evaluated for the proper maintenance frequency and type, the philosophy rings true for all—maintenance saves energy.
Regardless of market sector and maintenance strategy (run to fail, preventative, predictive), care must be given to allow for equipment maintenance to be performed. A way to achieve this during design is utilizing the philosophy of Design for Maintenance.
Design for Maintenance
Design for Maintenance aims to reduce the difficulties and costs associated with maintaining equipment. A maintenance-centric design takes into consideration the operation and future maintenance of equipment. In short, the philosophy takes into account what is required to maintain the equipment in question and allows enough room to execute the maintenance strategy.
Benefits of Design for Maintenance include a lower cost environment with fewer mistakes that reduce downtime and keep everyone safe. This recipe facilitates proper maintenance for the equipment, thus enabling operation at its intended performance and energy consumption benchmarks.
Putting Design for Maintenance Into Practice
An application of Design for Maintenance is clearance requirements. During my career, I had the privilege of mentoring under a very experienced engineer who came up the ranks in a plant environment with an active maintenance department. He taught me a simple lesson I call the “Bucket Principle”—leave enough room under rotating equipment for a maintenance person to sit and perform maintenance activities in an ergonomic way. Then it would not be tempting for someone to forgo the maintenance activity because it was hard to do or that it put the person in an uncomfortable position to work. Ironically most maintenance people at this plant carried tools in a five-gallon bucket that they would turn over and sit on. You would be surprised at the efficiency and runtimes achieved using the Bucket Principle.
Some equipment cannot be maintained in place and must be moved to be worked on. Taking the time to understand the client’s general maintenance practices can illuminate opportunities to increase safety and accessibility. While serving as Engineering Maintenance Manager at a chemical processing facility, I heard countless complaints of impossible requests for maintenance on equipment whose components could not be removed safely. Many of them were warranted.
In one instance, the designer had efficiently squeezed a new homogenization circuit into the already crowded space. The homogenization bin agitator was effectively installed on an elevated platform, which took into consideration operations and maintenance access, but did not take into account having to remove or repair wear items. Since space was tight, a single ladder was installed for access to the agitator bin platform. This circuit was already determined to require agitator blade replacement at a certain frequency. The 75 lb. shaft and blade assembly could easily be removed from the bin onto the platform, but getting the shaft down to the ground so it could be transported to the maintenance area was cumbersome. I do not know many people who can climb a ladder while holding a 75 lb. shaft in one hand, nor do I know anyone who could do that safely while maintaining three points of contact. The steps developed to remove it included constructing scaffolding platforms in a way to lug the shaft out and down to the floor, then transport it to the maintenance area via fork truck. This meant a day and half downtime.
The solution included stiffening the homogenization structure to accommodate an electric hoist. After that, one person could remove and replace the shaft within an hour or two. Had the designer taken the time to understand the maintenance requirements for the homogenization circuit, the structure could have been built with capacity for a hoist and would have saved thousands of dollars of re-design and downtime.
If you utilize a consultant to assist with design services at your site, consideration of how the equipment will continue to operate at its originally intended benchmarks should be a priority. For a successful project, it is imperative that your consultant understands the needs of all your internal stakeholders. Our team here at Progressive Companies understands the Design for Maintenance philosophy and have team members intimately familiar with what is required for your facility to run at its optimum energy efficiency and capability.
References:
“In 2018, U.S. Energy Expenditures Increased for the Second Consecutive Year.” Homepage - U.S. Energy Information Administration (EIA), www.eia.gov/todayinenergy/detail.php?id=45076#:~:text=U.S.%20total%20energy%20expenditures%2C%20the,Energy%20Data%20System%20(SEDS). Accessed 17 Aug. 2023.
Cousineau, M. (2020) 5 ways to reduce energy use with good maintenance, Fiix. Available at: https://www.fiixsoftware.com/blog/5-ways-to-reduce-energy-with-good-maintenance/ (Accessed: 17 August 2023).